正航技术编辑粉末渗铬用高温炉设备
正航技术编辑粉末渗铬用高温炉设备
1 粉末渗铬用高温炉;粉末渗铝用中温炉;粉末渗锌宜用可倾斜的鼓形炉,也可用带风扇的低温炉。
1.1应配备温度控制装置,温度控制精度应达到±10℃。
1.2加热炉有效加热区的温度均匀性应为±10℃。
1.3渗箱(罐)用耐热钢制成,渗铬、渗铝罐可带通保护气体的导管。
2.渗剂
渗剂的技术要求应符合ZB J36 014 的有关规定。渗剂组成见表 2。
3.工艺及后处理
3.1渗前准备
3.2根据图样的要求确定工艺参数。
3.3工件外观不应有锈迹、碰伤和裂纹,表面一般需磨削加工,且清洗干净。
3.4按配比配制好渗剂,搅拌混匀,置于 150~200℃烘箱中烘 1~2 h。渗箱(罐)、工件均应烘干。
3.5装箱时,工件与工件、工件与箱壁之间应留有 10~20 mm 的距离,将检验用的试样放在不同的位置。小渗箱放 1 个,大渗箱放 2~3 个,加盖后用水玻璃加耐火泥密封。
3.6 渗箱(罐)壁与炉子后墙或炉底应保持 150~200 mm的距离,与炉门应保持 200~250 mm的距离。
3.7渗金属工艺
3.8粉末渗金属温度、时间和冷却方法见表 3。计算保温时间应考虑渗箱(罐)透烧时间。
3.9粉末渗铬剂重复使用 4~5 次后,应补加 20%新渗剂,卤化铵按渗剂总量及配比追加;粉末渗铝剂使用 3~5 次后应补加 15%~20%的新渗剂,渗锌剂用若干次后应及时补加新剂。
4.后处理
4.1工件出炉、开箱后应清理干净。
4.2 渗铬、渗铝后的热处理,一般可选用其基体材料的工艺。渗铬后应先正火再淬火、回火。淬火、回火应符合JB 3877 的有关规定。
4.3渗锌后,一般工件在 150~160℃的机油中加热 1 h,也可直接喷涂料。
5.质量检验
5.1外观
渗件表面色彩应均匀、光洁,无裂纹、剥落、腐蚀斑等缺陷。渗铬后表面呈银白色,渗铝后呈银白色或银灰色,渗锌后呈银灰色。
5.2表面硬度
表面硬度测定按GB 9790 的规定。硬度允许偏差不应超过表 4 的规定。试验力应符合JB/T 5069
的规定。不同渗层试验力的选用见表 5。

1 粉末渗铬用高温炉;粉末渗铝用中温炉;粉末渗锌宜用可倾斜的鼓形炉,也可用带风扇的低温炉。
1.1应配备温度控制装置,温度控制精度应达到±10℃。
1.2加热炉有效加热区的温度均匀性应为±10℃。
1.3渗箱(罐)用耐热钢制成,渗铬、渗铝罐可带通保护气体的导管。
2.渗剂
渗剂的技术要求应符合ZB J36 014 的有关规定。渗剂组成见表 2。

3.工艺及后处理
3.1渗前准备
3.2根据图样的要求确定工艺参数。
3.3工件外观不应有锈迹、碰伤和裂纹,表面一般需磨削加工,且清洗干净。
3.4按配比配制好渗剂,搅拌混匀,置于 150~200℃烘箱中烘 1~2 h。渗箱(罐)、工件均应烘干。
3.5装箱时,工件与工件、工件与箱壁之间应留有 10~20 mm 的距离,将检验用的试样放在不同的位置。小渗箱放 1 个,大渗箱放 2~3 个,加盖后用水玻璃加耐火泥密封。
3.6 渗箱(罐)壁与炉子后墙或炉底应保持 150~200 mm的距离,与炉门应保持 200~250 mm的距离。
3.7渗金属工艺
3.8粉末渗金属温度、时间和冷却方法见表 3。计算保温时间应考虑渗箱(罐)透烧时间。
3.9粉末渗铬剂重复使用 4~5 次后,应补加 20%新渗剂,卤化铵按渗剂总量及配比追加;粉末渗铝剂使用 3~5 次后应补加 15%~20%的新渗剂,渗锌剂用若干次后应及时补加新剂。
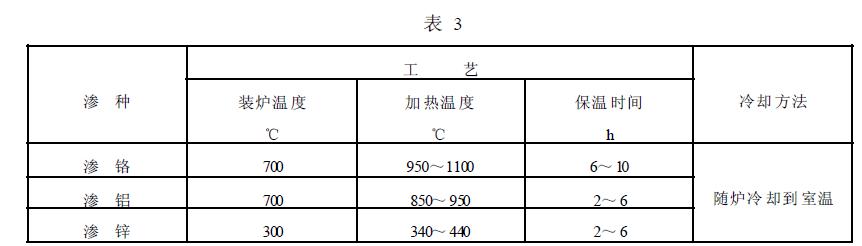
4.后处理
4.1工件出炉、开箱后应清理干净。
4.2 渗铬、渗铝后的热处理,一般可选用其基体材料的工艺。渗铬后应先正火再淬火、回火。淬火、回火应符合JB 3877 的有关规定。
4.3渗锌后,一般工件在 150~160℃的机油中加热 1 h,也可直接喷涂料。
5.质量检验
5.1外观
渗件表面色彩应均匀、光洁,无裂纹、剥落、腐蚀斑等缺陷。渗铬后表面呈银白色,渗铝后呈银白色或银灰色,渗锌后呈银灰色。
5.2表面硬度
表面硬度测定按GB 9790 的规定。硬度允许偏差不应超过表 4 的规定。试验力应符合JB/T 5069
的规定。不同渗层试验力的选用见表 5。
